광산장비의 친환경 스마트 기술혁신
목차
1. 광산장비의 특성 및 기술범위
2. 국내외 산업 및 기술동향
3. 시사점 및 정책제안
1. 광산장비의 특성 및 기술범위
광산의 정의
★ 광산장비(Mining Equipment)는 광물을 채취하는 장비
★ 광물을 채취하는 과정은 천공(Drill)→발파(Blast)→적재(Load)→운송(Haul)→분쇄(Crush)
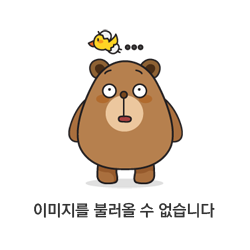
★ 천공공정은 노천 또는 지하광산에서 광석 또는 암석에 구멍을 뚫는 공정으로 발파품질에 결정적인 역할
★ 발파공정은 발파공(발파하기 위해 뚫은 구멍)에 폭약을 삽입하여 광석 또는 암석을 부수는 공정으로 환경과 안전이 중요
★ 적재공정은 1차 파쇄된 암석 또는 광석을 적재장비(굴착기, 로더 등)를 이용하여 운송장비(덤프트럭, 이송장치)에 적재하는 공정
★ 운송공정은 1차 파쇄된 암석 또는 광석을 크러셔 또는 하역장으로 운반하는 공정
★ 분쇄공정은 1차 파쇄된 암석을 일정한 크기로 분쇄하는 공정으로 폐기되는 부산물 없이 활용 가능한 다양한 크기의 광석 또는 암석을 추출
천공과 발파의 상관관계
★ 채굴(채광 또는 채석)현장은 발파대상의 특성(암석 물성, 절리군, 지하수 상태 등)과 채굴 프로세스 비용(그림 2)을 검토하여 가장 적절한 암석 크기 분포를 찾은 후 천공 및 발파 계획 최적화(그림 3)를 수행
★ 천공과정에서 천공 계획을 준수하지 못하고 천공위치, 깊이, 경사각 등에서 편차가 발생(그림 4)하면 부서진 암석은 균질하지 못하고 특히 비정상적으로 큰 암석은 브레이커 등을 이용하여 파쇄작업이 진행되며 시간과 비용 상승이 발생
★ 불량한 천공직진성은 두 가지 문제를 발생
- 벤치(bench) 바닥에서 횡간격(space, S)과 종간격(burden, B)이 너무 크면 벤치 바닥의 간극이 너무 커서 발파된 암석의 크기가 커지고
- 벤치(bench) 바닥에서 횡간격과 종간격이 너무 작으면 암석의 크기가 작아져서 발파 시 너무 멀리 날아가 안전을 위협할 수 있음
- 일반적으로 천공직전성이 양호하면 횡간격(space, S)과 종간격(burden, B)을 20% 넓힐 수 있고 이는 암석 생산량을 최대 20% 늘어나고 비용을 20% 절약 가능
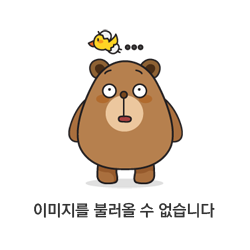
적재와 운송의 상관관계
★ 광산 운영과 비용의 관점에서 적재와 운송은 가장 중요
★ 광물을 채취하는 과정에서 적재 및 운송비용은 약 25-30%를 차지
★ 노천광산의 경우에 운송비용이 전체 운영비용에서 50-60%는 차지하는 경우도 있음
★ 운송비용을 줄이기 위하여 적재장비와 운송장비의 플릿연구가 진행 - 자율 또는 전기식 채광/운송 장비 도입
- 적재장비의 대기시간(Waiting Time) 최소화, 운송장비의 주기시간(Cycle Time) 최소화, 운송장비의 대기시간 최소화(그림 5)
- 적재 및 운반 차량 최적화 프로그램 운영
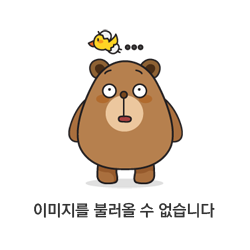
천공장비
★ 천공장비(그림 6)는 회전력과 충격력을 이용하여 암반에 구멍을 뚫는 장비이며 천공방식은 지표면 천공(Surface Excavation)과 지하 천공(Underground Excavation)으로 구분
- 천공장비 가운데 지표면 천공기로는 Top Hammer Drilling(THD)과 Down-The-Hole(DTH) Drilling 그리고 Rotary Drilling가 있음
※ THD는 20m 미만의 지표면 천공작업에 사용되며 노천광산, 지표면 토목공사에 사용됨, 지표면 천공장비 시장의 70%를 점유
※ DTH Drilling은 최대 4km까지 천공작업이 가능하며 광산, 자원탐사, 수자원공사, 토목공사, 석유/천연가스 등 다양한 작업에 사용됨. 지표면 천공장비 시장의 27%를 점유
※ Rotary Drilling은 주로 깊은 시추공을 획득하거나 암석 샘플을 채취하는데 사용되고 있으며 깊은 천공깊이(최대 10,000m)와 큰 천공경(100-610mm)의 천공작업에 사용
- 지하 천공장비로는 점보드릴(Jumbo Drill)과 승갱 굴착기(Raise Boring) 등이 있음
※ 점보드릴(Jumbo Drill) 장비는 터널의 천공발파 작업에는 THD 붐이 2~3개인 점보드릴이 대부분 사용되며 복수의 발파공을 4m까지 천공한 후 발파하는 방식으로 터널굴착이 진행
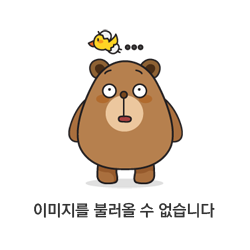
★ 천공기(그림 7)는 크게 Engine, Power Divider, Hydraulic Pump, Air Compressor, Dust Collector, Control Valve, Monitoring&Control System과 구조물 등으로 구성된 본체, 천공리그모듈, 제어모듈로 구성
★ 천공리그모듈(Drilling Rig Module)은 천공작업을 수행하기 위한 회전력과 충격력을 발생시키는 타격부(THD: Drifter, DTH: DTH Hammer, Rotary Drilling: 없음)와 타격부를 지지하고 이송시키는 Mast와 Feed Drive, 천공 공구 등으로 구성
★ 천공공구(Drill Tool)는 천공리그모듈에 장착된 드리프터에 조립되어 암반에 직접 구멍을 뚫는 작업을 수행하는 소모품 으로써 Shank Adapter, Coupling, Extension Rod, Drill Bit 등으로 구성
★ 제어모듈은 각각의 천공공정을 제어하는 모듈로서 핵심 서브모듈은 다음과 같음
- Hole Navigation System(HNS): 천공 계획에서 제시한 천공위치로 안내하거나 제어하는 모듈
- Rig Control System(RCS): 리그를 제어하는 모듈 - Auto Rod Handling System(ARHS): 목표 천공 깊이에 도달하는 과정에서 자동으로 드릴로드 추가하거나 목표 천공위치에 도달했을 때에 자동으로 드릴로드를 추출하는 모듈
- Auto Feed Fold(AFF): 작업 준비단계에서 피드를 트래밍(tram) 위치에 놓거나 작업 준비 위치로 자세잡는 모듈로서 작업 및 운송 중에 시간을 절약하고 리그 캐빈의 손상을 방지
- Auto Positioning of the Feed(APF): 리그 피드를 반자동 정렬하는 모듈로서 리그 자세의 정확도를 향상시켜 더 나은 품질의 암석을 생성
- Measure While Drilling(MWD): 천공과정을 인식 측정하는 모
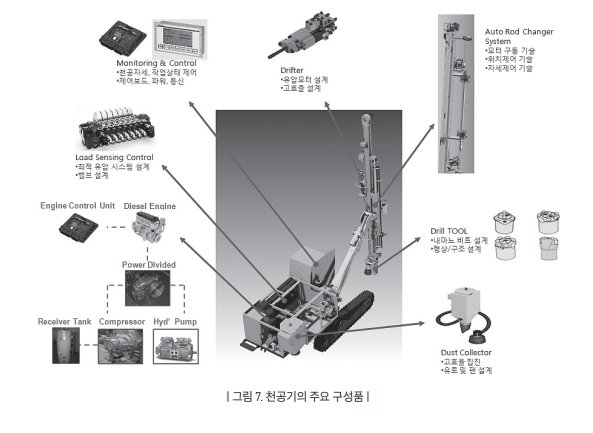
★ 스마트 천공기
- 스마트천공기(그림 8)는 운전자 보조 또는 자율기능을 이용하여 천공작업과 주행을 수행
- 천공작업
* 운전자는 천공작업을 할 때에 경험과 육안으로 비트 끝단의 위치를 확인하는 동시에 천공 깊이와 경사를 기계식 측정기로 추정 하고 있어 정밀 시공은 매우 어려운 실정
* 정밀 천공작업을 위해서는 천공 계획에서 요구한 천공을 목표로 스트링 라인을 천공 경사도와 일치한 상태에서 직선 천공을 수행
- 주행
* 노천광산에서 저속(4km/hr)의 천공기로 작업장을 이동할 때에 운전자는 심한 피로와 위험을 동반
* 피로와 위험을 회피하기 위하여 원격제어, 군집제어, 자율주행이 요구됨
* 기지국에서 천공 작업장 내에 위치한 개별 천공위치로 천공기를 이동
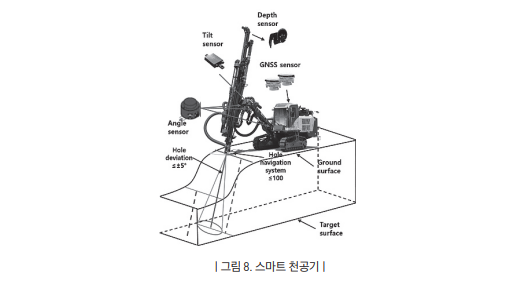
- 운전자보조 또는 자율화 구현 프로세스
* 주행/작업환경의 인식 과정(그림 9): LiDAR, RADAR, 카메라 모듈, 초음파 모듈 등을 이용하여 고정 또는 변동하는 외부의 사물 정보(거리, 속도, 크기 등)을 인식하고 GNSS 모듈, IMU, 각도센서 등을 이용하여 천공기의 정보(천공기 위치와 속도, 작업기의 변위와 속도 등)를 인식
* 주행/작업환경의 인지와 계획 과정(그림 10): 주행/작업 환경을 감지한 후에 사물의 상태를 인식하고 예측하여 주행 또는 작업 전략(장애물 회피, 천공작업 경로 등)을 수립
* 주행 또는 천공작업 전략에 따라 차량을 제어하는 과정: 상위/하위 제어기를 이용하여 차량제어
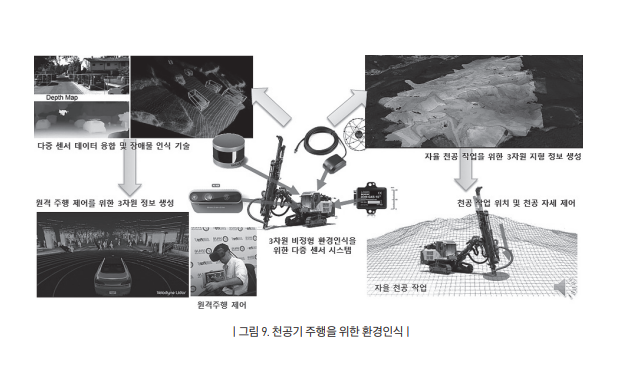
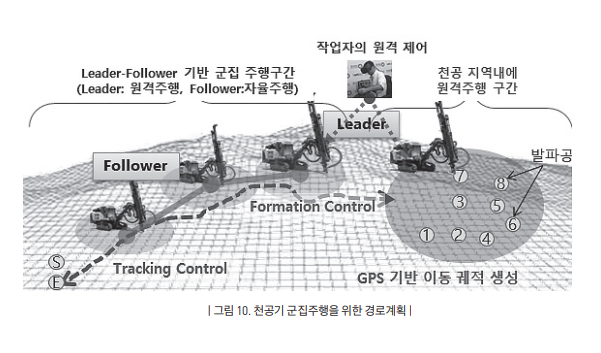
적재와 운송장비
★ 적재와 운송장비로는 굴착기(Excavator)와 로더(Loader)와 트럭(Truck) 등이 있음
- 노천 광산에서 사용되는 굴착기와 로더는 토공장비와 동일(그림 11)
- 지하 광산에서 사용되는 트럭은 낮은 차체 높이와 생산성을 높이기 위하여 고속의 선회속도, 인체공학적 운전석, 안전하고 빠른 타이어 교체를 위한 통합 재킹시스템(Integrated jacking system) 그리고 지능형 제어시스템 등 다양한 스마트 기능을 갖고 있음(그림 12)
- 지하 광산에서 사용되는 로더는 자동화와 연결기술 등을 포함한 스마트 기능과 배기가스가 없는 전기구동 방식을 적용
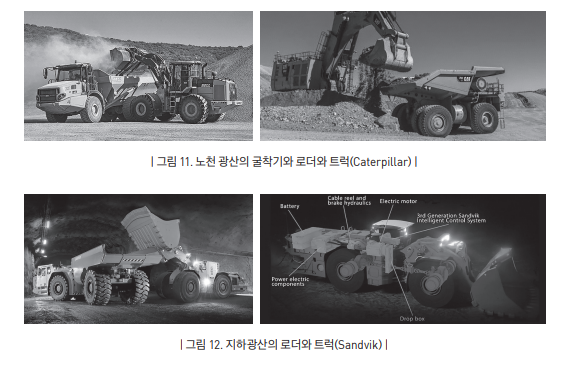
분쇄장비
★ 암석 파쇄와 규격골재 선별을 위한 장비로는 크러셔와 선별기 등이 있음
- 크러셔(Crusher)
* 크러셔(그림 13)는 채석장이나 광산, 토목/도로공사 현장에서 발생되는 암석이나 건설폐기물 현장의 폐 콘크리트 등을 파쇄하여 다양한 크기의 골재를 생산하는 장비로서 용도와 공정에 따라 죠, 콘, 임팩트 크러셔 등으로 구분되며, 크러셔의 파쇄 공정을 거친 암석은 100mm 이내의 일정 크기의 골재로 생산
* 크러셔는 정치식(Plant Type), 자주식(Mobile Type) 및 견인식(Potable Type)으로 구분되며, 정치식의 경우 기초공사를 통해 지면에 고정시켜 골재를 생산하며, 견인식은 트레일러 등으로 견인이 되는 이동이 가능한 방식의 크러셔를 뜻함
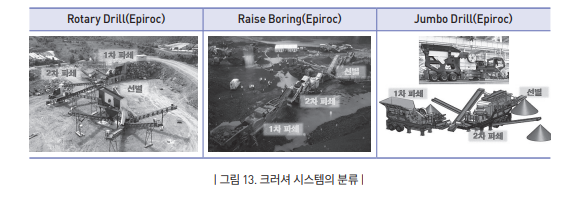
- 자주식 크러셔(Mobile Crusher)는 하부주행 장치가 적용된 크러셔로, 자체 주행이 가능한 완성차로서 주행차체의 상부에 골재 파쇄 및 규격골재 생산을 위한 죠 및 콘 크러셔 모듈이 탑재되는 형태
* 차체는 크롤러 트랙과 디젤엔진, 유압모터, 펌프로 구성이 되며, 상부 생산장비로 원석 이동을 위한 피더, 호퍼, 그리고 암석 파쇄를 위한 핵심부품인 죠 및 콘 크러셔 모듈이 탑재됨33
- 크러셔 시스템은 암석의 1차 파쇄를 위한 죠 크러셔(Jaw Crusher)와 타격 크러셔(Impact Crusher) 그리고 1차 파쇄된 암석을 골재화 시키는 2차 파쇄용 콘 크러셔(Cone Crusher)로 세분화되는데 콘 크러셔의 파쇄 간극 설정 등 운용조건에 따라 골재의 최종 크기 및 품질이 결정됨
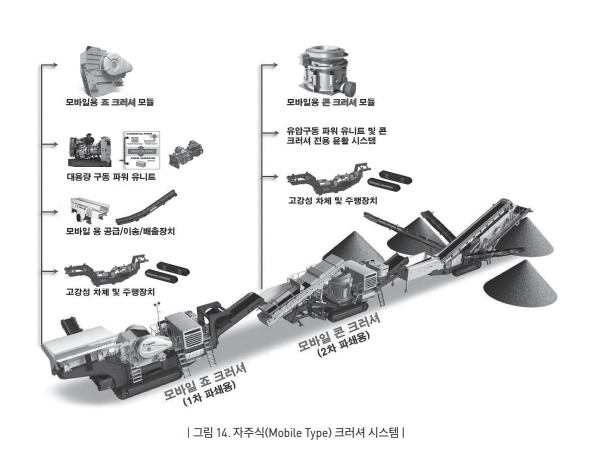
- 선별기(Screen) * 선별기는 크러셔 공정을 거친 다양한 크기의 골재나 광물 또는 토사, 환경 폐기물 등을 일정한 크기의 망으로 골재를 분류하는 장치로 스크린 공정을 거친 골재는 25mm 이하, 25-40mm, 40mm 이상 등으로 선별됨
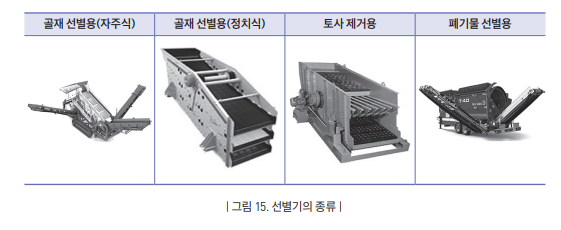
스마트 플랫폼
★ 원격제어 시스템 - 공간과 환경의 제한 없이 작업을 수행할 수 있도록 원격 제어 가능한 시스템으로서 원격제어기 또는 원격제어 스테이션, 운영 소프트웨어 그리고 실시간 영상과 센서 데이터 전송 시스템을 포함
- 원격제어기
* 작업자가 천공기 인근 또는 원거리에서 안전하고 편안하게 작업이 가능
* 통신 인프라가 필요하지 않고 최대 400m 거리에서 현장 작업을 수행
* 900MHz 또는 2.4GHz 주파수 통신 프로토콜을 사용
- 원격제어 스테이션
* 운전자는 익숙한 제어 장치와 장비 디스플레이가 있는 가상 운전실에서 원격으로 작업
* 작업자 입력이나 천공기의 상태정보는 전용 무선 송신기/수신기를 통해 원격 스테이션으로 전송되어 실시간으로 정확한 제어가 가능
* 고품질 비디오는 천공작업 영역을 명확하게 보여줌
* 운전자는 여러 대의 천공기를 전환해 가며 조정 가능하여 대기 시간없이 작업 현장 변경 가능
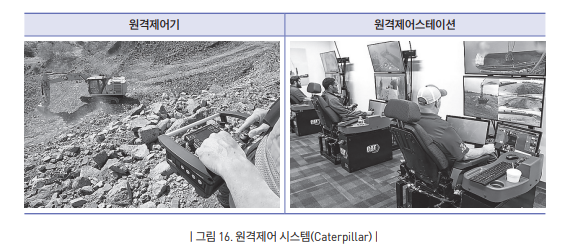
★ 관제 시스템
- 다양한 센서(GNSS, Lidar, IMU, Angle sensor, 유압센서 등)로 측정된 데이터를 가공하여 필요 데이터(장비 위치 정보, 완료된 작업 실적정보, 장비 건강정보 등)를 생성하고, 데이터를 관제소와 원격제어 스테이션 그리고 장비에 제공
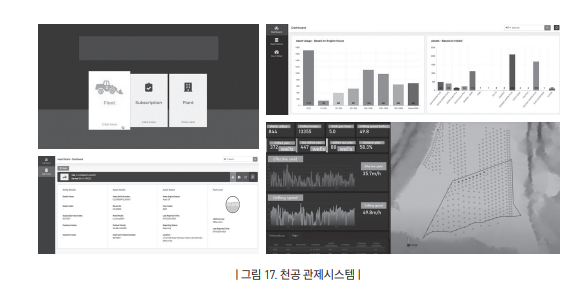
★ 플릿 관리시스템(Fleet Management System, FMS)
- 플릿 관리시스템은 1980년대에 차량에 컴퓨터가 탑재되고 위성과 지상파를 통해 네트워크로 연결되면서 시작됨
- 자동화와 비즈니스 프로세스의 최적화 관점에서 플릿에 연결된 차량을 관리하고, 파견, 구매, 통신, 네비게이션, 회계 및 재무와 같은 모든 비즈니스 부문을 단일로 연결하는 기술 솔루션을 의미함
- 일반적인 플릿 관리시스템이 운영되는 과정을 보면 제어센터에서 무선 네트워크를 이용하여 장비로 신호를 보내면, 장비는 데이터(위치, 탑재량, 광석 품질, 비용 코드 등)를 제어센터로 송출하고, 제어센터는 무선 및 위성 네트워크를 이용하여 이 데이터를 공유
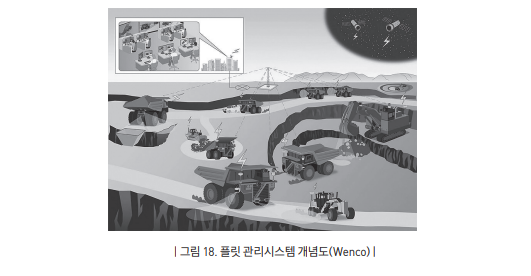
2. 국내외 산업 및 기술동향
산업동향
★ 세계 광산시장
- 세계 광산장비 시장규모를 보면 2019년에 1,217억불에서 2027년에는 1,658억불로 연평균 5.7% 성장할 것으로 예상
- 광산 장비는 광물처리 장비(휴대용 및 고정식), 표면 채굴장비(덤프트럭, 도저, 굴착기 등), 지하 채굴장비(굴착기, 도저, 트럭 등), 천공기 및 브레이커, 선별기 및 크러셔(고정식, 이동식) 및 기타 장비로 구분
- 2019년 기준, 광산 장비의 시장점유율을 보면 광물처리장비 8%, 지표면 채굴장비 29%, 지하 채굴장비 28%, 천공장비 10%, 분쇄장비 15%, 기타 10%로 분포
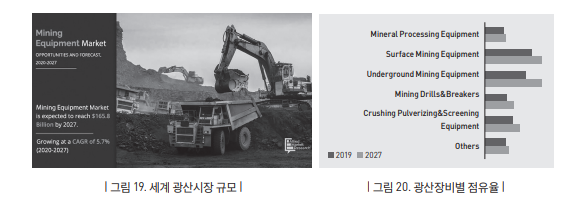
★ 세계 스마트 광산장비
- 스마트 광산장비의 시장규모는 2017년 22.2억불에서 2023년에는 32.9억불로 2017년부터 2023년까지 연평균 성장률 6.77% 수준으로 성장 예상
- 스마트 광산장비 기업은 시스템 통합기업, 소프트웨어 제공 기업, 장비 제공 기업, 통신 시스템 및 유통 기업으로 구성
- 스마트 광산 장비에서 지하채광 자동화장비와 자율 운반장비가 시장점유율이 높음
- 스마트 광산장비 대표 기업으로는 Atlas Copco(스웨덴), Sandvik(스웨덴), Hexagon(스웨덴), Caterpillar(미국), Autonomous Solutions Inc.(미국), Trimble(미국) 등이 있음
- 스마트 광산장비의 지역별 규모(그림 21)를 보면 2016년에 아시아 태평양이 가장 큰 점유율을 차지하고 있으며 앞으로도 전 세계적으로 채굴장비 및 채굴 자동화기술을 구현하기 위한 가장 큰 시장이 될 것으로 예측
* 이는 Rio Tinto, FMG Group 및 BHP Billiton과 같은 선도적인 탐사 및 채굴 회사의 자동화된 채굴 장비의 수요에 기인
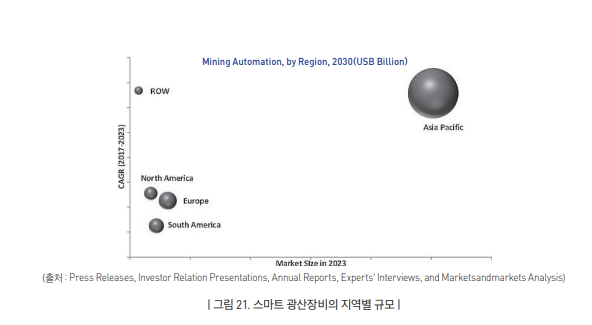
★ 천공장비
- 스마트 천공기의 경우에 유럽의 선진사(Epiroc, Sandvik)가 세계시장의 100%를 점유하고 있으며, 천공기의 스마트 기능 뿐 만 아니라 원격제어, 빅데이터, 플릿작업, 관제시스템 등을 포함하는 스마트 체계를 자체 개발하거나 M&A 또는 공동개발을 진행하고 있음
- Epiroc
* 2018년에 완전 자율 DTH 천공기(SmartROC D60 DTH)를 출시
* 2018년에 ASI Mining, LLC(미)을 인수하여 차량의 자율운영을 위한 기술 솔루션을 강화
* 2020년에 MineRP(칠레)를 인수하여 채굴 데이터와 머신 데이터 및 ERP 시스템을 통합하는 소프트웨어 플랫폼을 강화
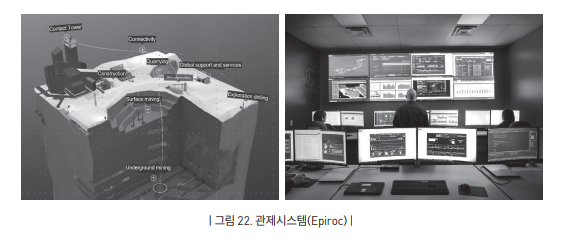
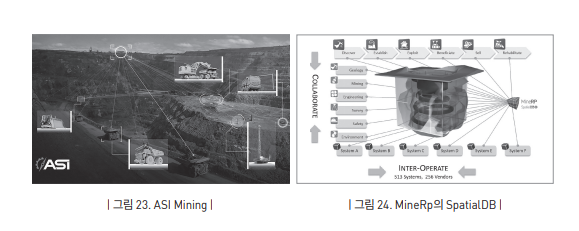
- Sandvik
* 2015년에 정밀 GPS와 카메라 등 센서를 채택한 완전 자율 회전식 천공솔루션(AutoMine Rotary Drilling)을 상용화하여 작업 목적지까지의 자율주행(Auto-Tramming) 및 자동화 된 작업 시스템을 구현
* 2019 년에 Artisan Vehicle Systems(배터리 구동식 전기 채굴 차량의 선도기업, 미)를 인수하여 배터리 전기 로더를 개발하였고 Newtrax(IoT 장치 제조 및 지하 채굴 안전 솔루션 공급)을 인수하여 지하광산의 전방위 플랫폼을 개발
* 2020년에 AutoMine® 시스템(AutoMine® Underground, 및 AutoMine® Surface Drilling)을 개발하여 자동화와 원격제어와 플릿작업을 수행
* 2020년에 Exyn Technologies(미)과 파트너십을 체결하여 3D 광산 시각화, 위치 추적, 일정 관리, 작업 관리, 장비 모니터링 및 분석을 포함하는 자동화 및 원격 제어 솔루션을 제공 * 2021년에 자율 Top Hammer XL(THD 방식)과 LEOPARD™ DI650i(DTH 방식)을 출시
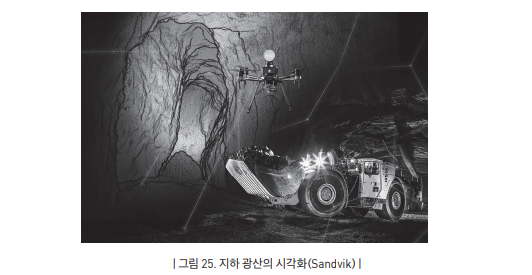
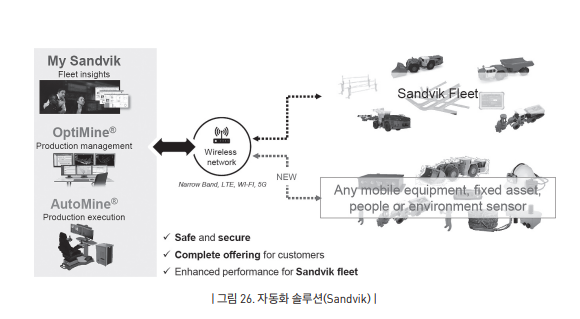
- 한국은 수산CSM과 수산중공업 그리고 에버다임에서 재래식 천공기를 생산 중에 있으며 최근에 스마트기술을 적용한 천공기를 개발 준비 중임
★ 운송 및 적재장비
- 적재 및 운송장비 경우에는 Caterpillar, Komatsu, Hitachi, Volvo, Scania, Sandvik 등 세계 선진사들이 세계 시장의 100%를 점유
- 2020년 2월까지 전세계 총 459대의 자율 주행트럭이 운영 중이며 수동 주행트럭에 비하여 1% 미만이지만 2019~ 2020년 동안에 매년 32%씩 폭발적 성장 중
- Komatsu는 1990년에 32톤 자율운송 트럭(HD320)을 연구개발을 시작하여 2008년에 자율운송시스템(Autonomous Haulage Systems, AHS, 그림 27)을 세계 최초로 Gabriela Mistral 구리 광산(칠레)에서 상용화한 이래 현재 9개의 광산 현장에서 약 150대가 운영 중. 또한 온실가스와 배기가스를 저감하기 위하여 완전 전기공급과 결합된 기술을 적용하는 3단계 전략(그림 28)을 수립
- Caterpillar는 Cat® MineStar(광산 운영 및 장비 관리를 목적으로 Fleet, Terrain, Detect, Health, Command로 구성)를 도입하여 호주, 브라질, 캐나다 및 미국에 위치한 9개 이상의 사이트에서 350대 이상의 자율 주행트럭(Cat 789D, 793D, 793F, 797F)을 운영
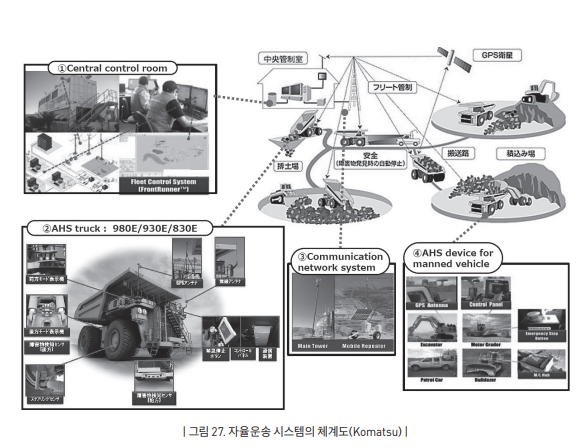
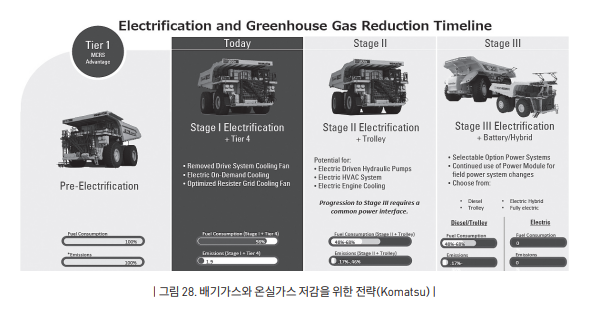
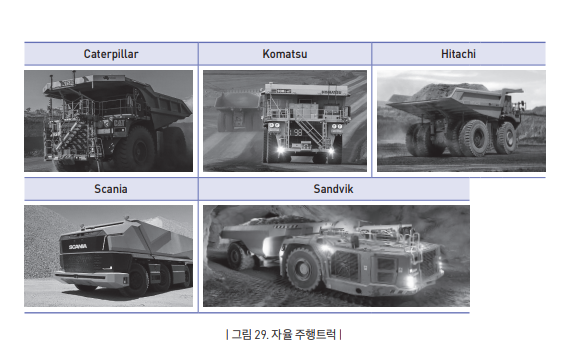
- 한국의 두산인프라코어와 현대건설기계는 운전자보조 기술와 자율작업 기술을 적용한 굴착기와 로더를 개발 중에 있으며 스마트플랫폼과 통합하는 프로젝트를 진행 중
* 두산인프라코어는 2020년에 건설현장 무인자동화 솔루션인 컨셉트-엑스(Concept-X) 프로젝트를 발표한 후 Xite Cloud(토공 현장 종합 관리솔루션)와 DoosanCONNECT(원격관리시스템)과 X-center(관제 시스템)를 구체화 중
* 현대건설기계는 원격관리시스템인 하이메이트(Hi-Mate)를 운영 중에 있으며 미래형 건설플랫폼이라 불리는 ‘스마트 컨스트럭션’을 개발 중
* 두산인프라코어와 현대건설기계는 2019년에 ‘머신가이던스’ 굴착기를 자체 개발해 상용화하였고 현재는 자율굴착기와 로더를 개발 중
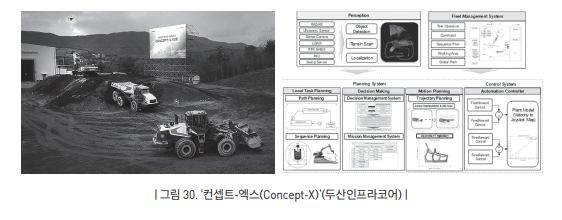
★ 크러셔
- 글로벌 시장에서 아시아 태평양 지역은 모바일 크러셔와 스크린의 시장 규모가 가장 높은 부분으로서 시장 점유율이 약 45% 정도로 추정되는데 이는 중국, 인도, 일본, 말레이시아, 호주 등이 가까운 미래에 인프라 개발에 대한 투자 증가 기대에 기인
★ 한국 광산장비 동향
- 국내 천공기는 매년 약 180대가 생산되고 있으며 생산 규모는 350억 원 가량으로 생산량의 약 70%가 해외 수출되고 있음 ★ 국내 크러셔 시장은 약 1,100억 원으로 추정되며, 사용연한에 의한 소모품의 교체나 기타 부품시장 등의 After market을 포함한다면 약 2,000억 원의 시장규모로 예상됨
★ 공공투자의 증대를 통한 민간부문의 도모 등 경기 부양책으로 2021년 하반기부터는 서서히 회복될 것으로 전망하고 있으며, 국내 골재 수요는 도시재생, 생활 SOC투자 및 토목, 건설 등의 수주 증가로 연평균 1.26%로 증가할 것으로 전망
스마트 기술동향
★ 광산 회사는 광물의 수요는 증가하고 있는 반면에 접근 용이한 광산은 대부분 사라지고 있으며, 광석 매장량 감소, 인건비 및 에너지 비용 상승, 작업자의 안전과 환경 보호를 위한 규제(CO₂배출저감, 물 사용 최소화 등)강화로 인해 어려움에 직면
★ 이러한 어려움을 해결하기 위하여 미래의 광산은 자율화된 무인 광산현장(zero-entry mining)을 구축하여 작업인력을 위험한 지역에서 안전한 장소로 재배치하고, 직원 채용이 쉬운 도심 지역에서 원격으로 광산 생산을 관제, 자율 운영과 예측 유지 보수를 지원
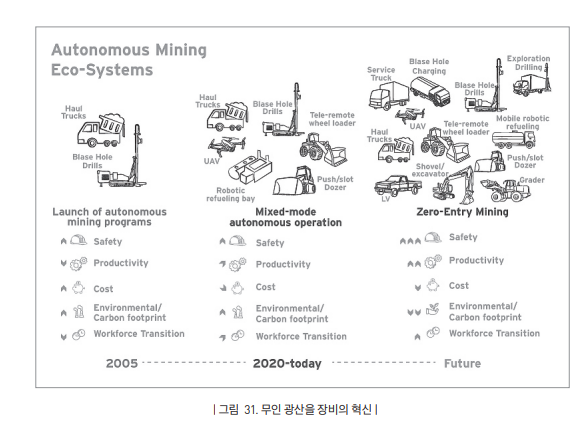
★ 2005년에 Codelco(칠레), Rio Tinto(호주) 및 BHP(호주)와 같은 선진 광산업계에서 채굴에서 운반에 이르는 통합 프로그램을 주도하면서 자율 건설 및 광산기계를 요구하기 시작함
★ 현재까지의 기술단계는 자율 채광 프로그램의 도입기(그림 31)의 Launch of autonomous mining programs)에 해당 하며 채굴 프로세스의 단계별 공정에서 기존 장비에 스마트 기능을 부여하는 단계
★ 현재 진행 중인 기술단계는 자율 채광 프로그램의 중간기(그림 31)의 Mixed-mode autonomous operation)에 해당 하며 자율 장비에 원격제어와 플릿 관제시스템과 연결기술 등을 도입하여 단계별 공정의 장비와 작업자를 서로 유연하게 조정 및 결합하는 ‘플러그 앤 플레이(plug and play)’ 단계
★ 최종 기술단계는 작업영역 내에서 완전 무인 자율화하는 단계로서 극복해야 할 기술적 과제가 다수 - 미래의 스마트 광산(그림 32)은 모든 공정(천공 →발파 →적재 →운송 →파쇄)을 자율화하고 통합 관리 운영하는 체계로 진화
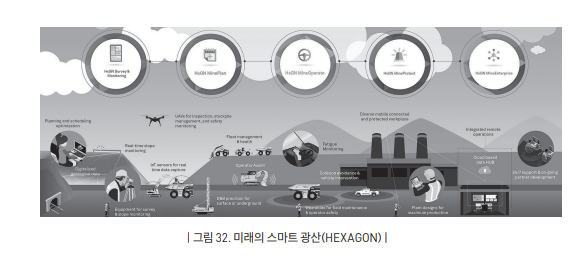
★ 자율 채광 프로그램의 도입기 사례: Rio Tinto 사의 채광 프로세스 운영 사례(그림 32)
- 2008년에 ‘Mine of the Future’를 선언하고 West Angeles에서 처음으로 ADS(Automatic Drilling System) 타당성 테스트를 성공적으로 수행
- 운영 장비:Automatic drilling system(ADS)이 장착된 20대 천공기, Autonomous Haulage System(AHS)가 장착된 100대 자율 주행 덤프(Komatsu 930E 덤프트럭 포함)
- 운영 특징:원격 작업자는 단일 콘솔을 사용하여 4개의 자율 천공기를 동시 제어하여 무인 완전 자동화된 홀 패턴 드릴링을 달성
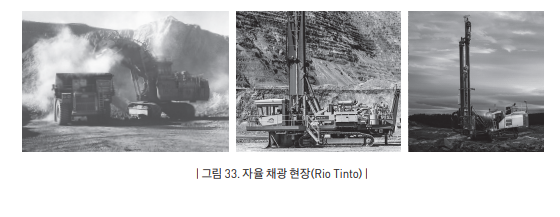
★ 자율 채광 프로그램의 도입기 사례: BHP사의 채광 프로세스 운영 사례(그림 34)
- 운영 장비 : Epiroc사의 Pit Viper 271 수직천공기
- 운영 특징 : 12 시간 교대로 11.5 시간 동안 총 15,000시간, 백만 미터 이상 자율 천공작업 수행. 드릴 최적화가 20% 개선되어 굴착, 적재 및 운반이 개선되고 장비 가동 시간이 증가
- 향후 계획: 20대 규모의 천공기를 초기에는 Pilbara에 있는 5개의 철광석 광산에서 나누어 원격 제어하고 장기적으로는 Perth 기지에서 통합 원격 제어 운영

★ 스마트 공통 핵심기술
- 스마트 핵심기술은 스마트 장비 기술과 스마트 플랫폼 기술로 구분됨
- 스마트 장비는 외부 주행 및 작업환경을 인식하고 이를 판단하여 주행 및 작업 전략을 수립하며, 장비를 제어하는 프로세스로 작동
- 스마트 플랫폼 기술은 스마트 장비들을 원격제어하고 플릿 관리 및 관제를 포함하는 디지털서비스가 있음
- 스마트 장비에 필요한 핵심기술은 자율 주행 자동차 관련 핵심기술과 유사하며 다음과 같음
* 레이더(라이더) 기반 정보융합형 주행 및 작업 상황인지 기술
* 영상 센서 기반 정보융합형 주행및 작업 상황인지 기술
* 확장성, 범용성, 보안성을 확보한 V2X(V2V&V2I) 통신 기술
* 보급형 고정밀 복합 측위 기술
* 운전자 수용성을 고려한 자율주행 및 작업 HVI(Human Vehicle Interface) 기술
* 안전한 자율주행을 위한 운전자 모니터링 기술
* 차세대 IVN 플랫폼 및 통합 제어기 기술
★ 천공장비의 기술동향
- 유럽 선진사는 1990년에 스마트 천공기술을 개발하기 시작하였음
* 2000년에 AtlasCorp(Epiroc의 과거명칭)가 1세대 RCS를 개발
* 2000~2001년에 점보드릴용 2세대 RCS 플랫폼은 출시
* 2002~2006년에는 다양한 기종(천공기, 로더, 탐사 리그 및 Robbins Raisebore)에 3세대 RCS 기반 장비가 출시
* 2007~2010년에 4세대 데이터 기반 RCS 플랫폼을 개발하여 Pit Viper 271와 같은 로터리 발파 천공장비에 상용화
* 현재는 5세대 RCS 플랫폼을 Epiroc의 일부 기종(SmartROC D65, PV-231 blasthole drill 등)에 적용하였음
- 현재 유럽 선진사의 스마트 기술을 보면 광산사무실 또는 천공기 운전실에서 천공계획을 프로그래밍한 후에 USB 또는 WLAN(무선 근거리 통신망)을 통해 프로그램 데이터를 천공기에 제공하여 자율천공을 수행
- 한국의 수산CSM, 수산중공업, 에버다임은 2010년에 이르러 운전자보조(Machine Guidance) 단계의 HNS와 RCS를 개발하였으나 나머지 스마트 천공기술은 전무함(표 1)
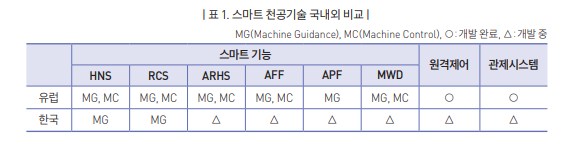
★ 적재 및 운송장비의 기술동향
- 최근에 광산현장은 생산성 증대와 비용절감과 안전 강화 그리고 환경 부담을 개선하기 위하여 자율운송 시스템을 도입하였으며 현재는 친환경·자율화·전기식·무인화·원격제어 기술로 진화하고 있음
- 자율운송 시스템은 자율운송 트럭과 관제시스템과 플릿 관리시스템 등을 통합한 관리운영 시스템임
* Caterpillar AHS는 Cat MineStar 솔루션(Fleet, Terrain, Detect, Health, Command)을 도입하여 실시간 정보를 통해 자재 추적, 충돌방지, 장비 상태 모니터링 및 자율 장비 시스템 관리를 수행
* Komatsu AHS는 Dispatch(플릿 관리시스템)과 FrontRunner(중앙 제어시스템)과 연계하여 무선 통신 네트워크를 기반으로 자율 운송 트럭과 적재 장비와 유인 차량을 통합관리 운영하고 있음. 특히 2019년에 세계 최초로 LTE 모바일 광대역 통신에서 무인화 운송기술을 구현(그림 35)
* Sandvik의 AutoMine Fleet Underground(Remote, Fleet, Access API, Lite, Multi-Lite)을 도입하여 로더 및 트럭의 자율 작업, 자율주행, 원격제어, 자동 임무 및 교통 제어 기능을 갖춘 다중 기계 제어 및 전체 차량 자동화를 구현하였고 OPTIMINE을 도입하여 지하 암석 채굴 생산 및 공정을 분석하고 최적화하기 위한 가장 포괄적인 솔루션 기술 개발
* 두산인프라코어와 현대건설기계는 5G 굴착기 원격제어 기술을 세계 최초로 공개하였음. 특히 두산인프라코어는 2018년 12월에 바우마 차이나 2018에서 880km, 2019년 4월에 바우마(BAUMA) 2019에서 8,500km 원격거리에서 제어를 구현
- 최근에는 인건비를 절감할 뿐만 아니라 작동 시간 연장(작업 휴식 및 교대 전환에 소요되는 시간 제거), 연료 소비 감소 및 장비 수명 연장과 사람의 실수를 줄인 안전성을 향상시키기 위하여 무인 적재 및 자율운송 기술이 개발되고 있음
- 지하광산에서 온실가스 저감과 작업자의 배기가스 노출을 배제하기 위하여 무인 전기 기술이 개발되고 있음
* Epiroc은 대형 탑재 하중 트럭에서 배터리와 트롤리를 결합하여 완전 전기 작동기술을 개발
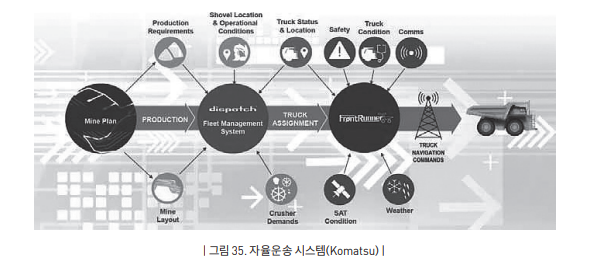
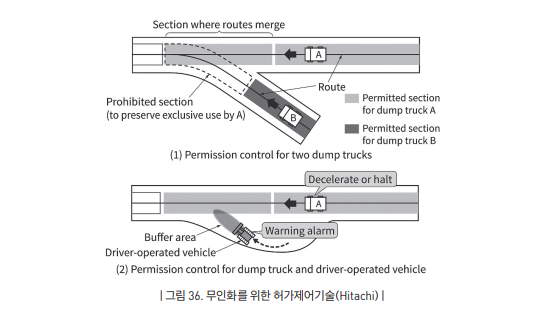
★ 분쇄장비의 기술동향
- 해외 선진사는 대용량 모바일 크러셔 제작기술과 골재생산 공정을 지원하는 파쇄 및 선별장비의 제작/설계 기술을 보유하고 있으며 골재 생산/선별 공정 자동화를 위한 제어기술과 암석파쇄 상태 모니터링 기술을 통한 건설현장의 골재 생산에 대한 통합공정 솔루션 제공을 위한 기술 개발 진행 중
* 현재 크러싱 플랜트 시장의 규모는 약 4:1의 비율로 전통 방식인 정치식 플랜트가 우위지만 운영의 효율성이 강조 되면서 점차 스마트화 지능화가 접목된 모바일 크러싱 플랜트의 공급이 늘어나는 추세
* 미국과 유럽의 선진 제조사를 중심으로 ICT, AI, 텔레매틱스, Dual power(전동/엔진 구동방식) 또는 Hybrid 등의 최신 기술이 접목된 중대형 모바일 크러싱 플랜트 개발이 증가
* 세계 크러셔 시장을 주도하고 있는 유럽, 미국의 선진사들은 폭 넓은 시장 확보를 위해 소/중/대형급의 크러싱 플랜트 Line up을 갖추고 있고, 자동차나 항공 산업에서 적용하고 있는 ICT, AI, Hybrid 등 최신 기술을 도입
- 국내 기업은 크러셔 장비에 필요한 기계적 분쇄기술을 확보하였지만 스마트기술은 전무(표 2)
* 삼영플랜트㈜에서 부하감지가 가능한 220톤급 모바일 죠, 콘 크러셔는 2018년도에 개발완료 하였지만, 지능형 제어 및 스마트 기술을 적용하지 못함
* 현재 국내에서는 400ton/hr 이상 골재생산이 가능하며, 암석 파쇄, 선별, 골재 생산 등 전(全)공정 자동화 모바일 크러셔 시스템 개발이 진행 중임
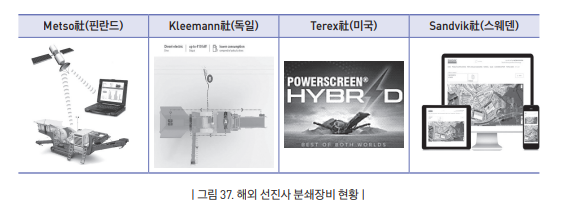
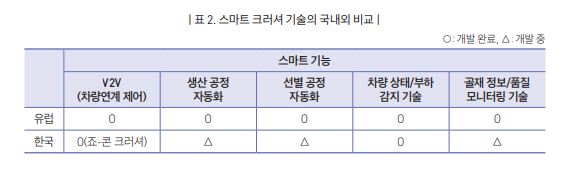
3. 시사점 및 정책제안
광산시장에서 스마트 기술 단계
★ 세계 광산시장은 생산성 증대와 비용절감과 안전 강화 그리고 환경 부담을 개선하기 위하여 자율화된 무인 친환경 광산현장(zero-entry mining)을 구축 중임
★ 현재의 스마트 기술 단계를 보면 해외 선진사는 ‘자율 채광 프로그램의 중간기’에 진입하였으나 국내 기업은 ‘자율 채광 프로그램의 도입기’의 진입 또는 진행 단계에 있음
- 선진 장비 제조회사는 광산시장의 니즈에 대응하기 위하여 친환경기술(Tier 5 디젤엔진, 전기·배터리)과 스마트기술 (자율화·무인화 기술)과 스마트플랫폼 기술(원격제어시스템, 관제시스템, 플릿 관리시스템)을 융복합하고 디지털 서비스를 구현
- 국내 대기업(두산인프라코어, 현대건설기계)은 선진 장비 제조회사와 유사한 스마트 체계를 구축 중에 있으나 중소· 중견기업(수산중공업, 수산CSM, 에버다임, 삼양플랜트 등)은 아직 스마트 체계 계획 중
광산과 융합한 기술개발 추진
★ 선진 제조기업과 한국의 대기업은 스마트 장비를 선도적인 탐사 및 채굴 회사와 스마트 장비 또는 체계를 실증하면서 기술 고도화를 달성하고 있음
- 선진사의 적재 및 운송장비(굴착기, 로더 등)는 1990년대부터 스마트 기술을 개발하기 시작하여 2008년에는 광산 회사에 투입하여 실증개시
- 한국의 적재 및 운송장비는 2010년에 스마트 기술을 개발하여 2018년에 실증을 개시
★ 향후 한국의 기업은 선진 제조기업과 경쟁하기 위해서는 친환경 동력원 기술(Tier 5 디젤, 수소 등), 스마트기술, 스마트 플랫폼 기술을 적용한 장비개발을 강화하고 탐사 및 채굴회사와 실증 협력 프로그램 개발 필요
스마트 기술 개발 지원
★ 친환경 동력원(전기·배터리, 수소) 기반 스마트 광산장비의 개발과 실증
- 광산은 다양한 장비가 집적화되어 운영되므로 단기간에 효율적으로 친환경 동력원의 운영방안을 수립하고 실증이 가능 ★ 한국의 중소·중견기업은 기술경쟁력을 강화하기 위하여 기보유 기술을 바탕으로 기종을 다변화하고 스마트 플랫폼 기술을 보유한 산학연과 협력하여 광산용 스마트 플랫폼 개발을 추진
- 스마트 점보드릴(친환경 디젤엔진 기반, 전기·배터리식 기반)은 지하광산에서 사용되는 수평천공기로서 기존 생산 중인 수직천공기와 기능과 기술이 유사하므로 국산화 개발이 용이
- 국내 대기업이 스마트 운송 및 적재 장비를 개발하는 과정에서 스마트 플랫폼의 기초기술 역량이 확보되었으며, 스마트 플랫폼 등 확보된 기술을 천공장비 또는 분쇄장비로 확산하는 연구개발이 필요
Big data를 활용한 디지털 서비스 기술 개발
★ 선진 장비 제조회사는 스마트 기술 상용화 과정에서 확보된 Big Data를 기반으로 다양한 디지털 서비스를 제공
★ 한국의 장비 제조회사 역시 Big Data를 활용한 디지털 서비스의 개발전략과 연구개발이 필요
출처 : keit pd 이슈리포트
'사회경제' 카테고리의 다른 글
국내 불소화학 산업 동향 (0) | 2023.03.19 |
---|---|
휴먼팩터 지능화의 디자인 기술동향과 산업전망 (0) | 2023.03.18 |
스마트공장을 위한 수직 통합패키지 개발 (0) | 2023.03.04 |
지능형 소성가공기술 동향 및 전망 (0) | 2023.03.03 |
광융합휴먼케어 기술동향과 산업전망 (0) | 2023.03.03 |
댓글