경량 소재 마찰교반용접 기술 및 장비개발 최신 동향과 적용 사례
<목차>
0. 요약
1. 마찰교반용접 기술의 개요
2. 기술 동향
3. 장비기술 및 시장 동향
4. 적용 사례 및 파급력
5. 정리 및 시사점
출처 및 참고자료
0. 요약
- 마찰교반용접은 고상용접의 한 종류로, 회전하는 툴에 의해 소재를 마찰가열 및 교반하여 용접부를 생성하는 기술이다. 이 기술은 주로 알루미늄 합금의 용접에 활용되며, 마그네슘 합금, 구리 합금, 티타늄 합금과 탄소강과의 이종접합도 가능하다. 마찰교반용접 장비는 소재에 접촉하여 용접을 수행하는 툴, 툴을 고속으로 회전시키는 스핀들, 그리고 툴을 이송하고 소재에 삽입하는 머니퓰레이터로 구성되어 있다.
- 장비는 머니퓰레이터의 유형에 따라 수직 다관절 로봇 기반 장비와 공작기계 기반 장비로 분류된다. 수직 다관절 로봇 기반 장비는 작업과 설치 공간에 대한 높은 유연성을 갖지만, 내압 사양이 낮고 힘 제어 기능이 필요하다. 공작기계 기반 장비는 높은 내압 사양과 변위 제어 및 힘 제어를 적용할 수 있지만, 툴 틸트각을 부여하기 위해서는 별도의 틸트헤드의 장착이 필요하다.
- 우주·항공산업에서는 마찰교반용접 기술이 우주발사체의 경량화를 위해 활용되며, 이는 Space X의 Falcon 9와 ‘아르테미스 계획’ 등에서 볼 수 있다. 자동차산업에서는 전기차로의 전환으로 배터리팩 부품과 인버터 등의 핵심 전력장치 보호에 마찰교반용접 기술이 활용되고 있다. 그러나 국내 마찰교반용접 기술과 장비는 아직 충분히 확보되지 않은 상태이며, 대부분 국내 장비와 기술시장은 해외 기업이 선점한 상태다.
- 마찰교반용접 기술에 대한 공정기술과 장비기술에 대한 개발은 늦었지만, 현명한 연구개발 전담 기관의 판단으로 곧 상용화를 앞두고 있다. 외산 기술과 장비 대비 시장 경쟁력을 충분히 갖춘다면 저렴하게 제작하는 기술이 필요해진 전기차시장에 동조하여 외산 기술의 의존 없이 국가 경쟁력을 향상시킬 수 있는 계기가 될 것이다.
1. 마찰교반용접 기술의 개요
기술 개요
- 마찰교반용접(Friction Stir Welding, FSW)은 1991년 영국의 용접·접합 관련 전문기술기관인 TWI (The Welding Institute)에 의하여 고안된 기술로, 소재의 용융 없이 용접하는 고상용접(solid welding)의 한 종류다.
- 마찰교반용접은 경로를 따라 이동·회전하는 툴(tool)에 의해 발생하는 소성 상태의 소재를 마찰(friction) 가열 및 교반(stir) 하여 용접(welding)부를 생성하는 공정기술로 정의된다. 회전하는 툴의 경로 이동 없이 한 지점만 용접을 수행하는 경우 마찰교반점용접(Friction Stir Spot Welding, FSSW)으로 명명한다.
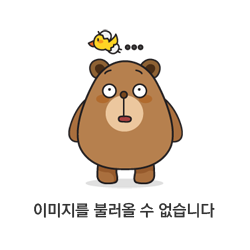
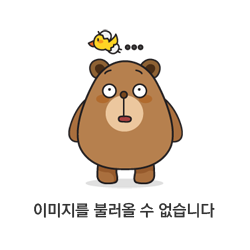
- 기존 아크용접이나 레이저용접 기술과 같은 용융용접(fusion welding)과 달리 소재의 녹는점 이하에서 수행함으로 고상용접이 가지는 장점인 낮은 에너지 소모, 높은 에너지 효율, 적은 용접변형과 함께 분진, 가스등의 사용과 생성이 없어 친환경적인 용접기술로 평가받고 있다.
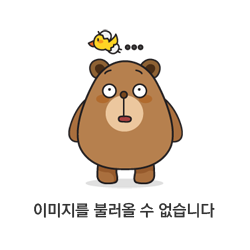
- 주로 용융용접기술로 결함 없는 용접부 제조가 어려운 알루미늄 합금의 용접기술로 활용된다. 마그네슘 합금이나 구리 합금의 용접 및 티타늄 합금과 탄소강과의 이종접합도 가능하여 경량 소재의 적용이 확대되는 최근 산업계의 동향과 함께 수요처와 적용처가 확대되고 있다.
- 특히 마찰교반용접 기술의 특허 기간이 만료된 이후 2010년대 중반부터 상업적인 활용이 시작되었으며, 현재 다양한 파생 기술의 형태로 철도, 우주·항공, 자동차산업에 활용되고 있다. 특히 국내 산업에서는 전기차 부품을 구성하는 용접기술로 주목받고 있으며, 폭발적인 기술 확산의 계기가 되었다.
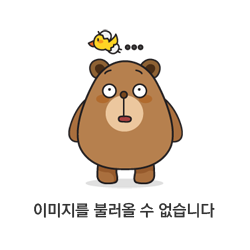
관련 표준
- 마찰교반용접 기술에 대한 대표적인 국제표준은 알루미늄에 대한 마찰교반용접(ISO 25239), 알루미늄에 대한 마찰교반점용접(ISO 18785), 항공·우주용 알루미늄 합금의 마찰교반용접 사양(AWS D17.3) 등이 있다.
- ISO 25239와 AWS D17.3은 동일한 현상과 기술에 대하여 다른 기준과 용어를 제시하고 있으므로 표준 활용 때 혼동을 주의해야 한다. 가령 그림 5와 같이 ISO 25239-1에서는 하나의 숄더와 프로브가 일체로 제작된 툴을 활용하는 방법을 마찰교반용접으로 명명하는 반면, AWS D17.3에서는 기존 마찰 교반용접(Conventional friction stir welding, CFSW)으로 명명하고 있다. 본 보고서는 ISO 25239와 ISO 18785의 기준과 용어를 따라 서술하되, 필요한 경우 AWS D17.3의 용어를 활용하여 서술했다.
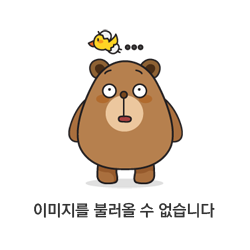
마찰교반용접 장비의 구성 요소 및 특징
- 고속으로 회전하는 툴을 소재에 압입하는 과정을 요구하는 기술로, 용접을 위해서는 기계화된 시스템이 필요하다. 시스템의 구성 요소는 크게 소재에 접촉하여 용접을 수행하는 툴, 툴을 고속으로 회전시키는 스핀들(spindle), 그리고 툴을 이송하고 소재에 삽입하는 머니퓰레이터(manipulator)로 분류할 수 있다.
- 툴의 소재는 용접하고자 하는 소재보다 높은 압축강도와 고온에서의 내마모성을 가져야 한다. 알루미늄 합금을 대상으로는 열간공구강인 STD61, 고속도공구강인 SKH51 등이 주로 사용되며, 마그네슘 합금 및 구리 합금을 대상으로는 초경합금이 사용되기도 한다. 티타늄, 스테인리스강, 고장력 강판 대상으로는 PCBN(Polycrystalline Cubic Boron Nitride)이 활용되기도 한다.
- 스핀들의 사양은 절삭용 공작기계에서 사용하는 스핀들의 회전속도와 토크 범위에서 크게 벗어나지 않으나, 툴을 소재에 삽입하고 삽입된 상태에서 이송하면서 발생하는 축 힘과 용접 방향의 반발하는 힘에 저항할 수 있는 내압 사양이 요구된다. 알루미늄 합금을 용접하는 데 요구되는 축 힘은 공정 조건에 따라 4~20kN, 반발 힘은 1~7kN이 발생한다.
- 마찰교반용접의 품질은 툴을 소재에 삽입하는 깊이에 크게 영향을 받는다. 따라서 툴이 장착된 스핀들을 이송하는 머니퓰레이터는 정밀한 3차원 이동이 가능해야 하며, 특히 삽입 방향(통상 z축이나 스핀들 축으로 명명되는) 정밀도는 0.1mm 이내가 되어야 한다. 아울러 스핀들이 요구받는 수준의 내압 사양이 필요하다.
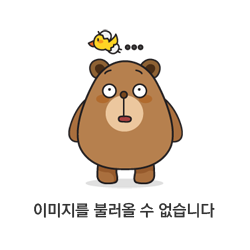
2. 기술 동향
툴 형상 설계기술의 동향
- 통상적인 마찰교반용접 툴(그림 4)은 프로브와 숄더로 구성된다. 프로브는 용접부를 직접적으로 교반하는 역할을 하고 숄더는 용접부 표면에 접촉하여 프로브의 교반이 용이하게 이루어지도록 열과 교반력을 부가해 주는 역할을 한다.
- 용접부의 품질 수준의 향상 또는 생산성의 향상을 위하여 툴의 형상은 다양한 형태로 설계할 수 있다. 일반적으로 실험을 통한 데이터베이스 및 수치해석 모델 등을 활용하여 툴을 설계한다. 툴의 형상을 설계하는 기술은 품질과 생산성을 결정하는 핵심적인 기술임에도 불구하고 형상과 관련된 고안은 특허 등 지식재산권으로 보호받지 못한다.
- 따라서 툴의 형상에 대한 정보는 관련 연구기관과 기업에서 공개하지 않고 있으며, 국내에는 발주처가 설계하여 공급하는 형태로, 해외에는 기성품의 형태로 툴이 공급되고 있다. 이때 해당 툴에 적합한 소재나 공정 변수 등 툴을 활용하는 방법에 대한 기술 서비스도 제공하고 있다.
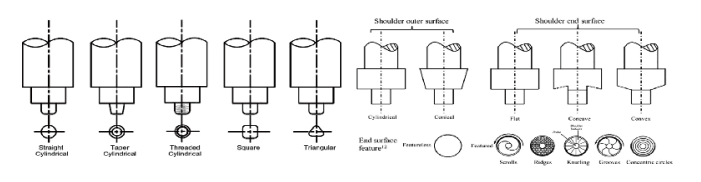
파생 기술의 동향
- 숄더와 프로브가 일체화된 툴을 사용하는 마찰교반용접 기술의 대표적인 제한점은 상대적으로 넓은 용접부 폭(통상적으로 용입 깊이의 4배), 용접부 반대 위치(이면)에 축 힘을 견딜 수 있는 내력 구조가 필요하다는 것, 출구 구멍의 잔존이다. 용접부 폭이 충분히 확보되지 않는 경우 결함이나 측면 파열이 발생한다. 또 이면 내력 구조가 없는 경우에는 용접부가 주저앉는 현상이 발생하며, 출구 구멍은 소재의 단면 감소의 원인이 된다. 이러한 제한점을 해결하기 위해 여러 가지 방법이 제안되었으며, 표준에 등재된 기술에 대하여 표 1로 정리하였다.
표 1. 마찰교반용접의 파생 기술에 대한 요약

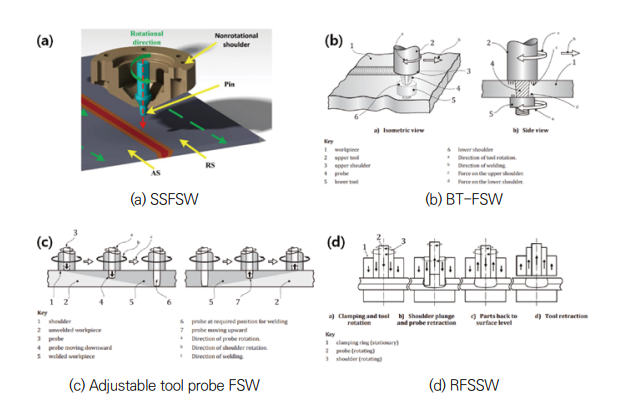
제어기술의 동향
- 마찰교반용접 기술의 저변이 확대되면서 툴의 삽입 깊이를 제어하는 기술이 장비에 탑재되고 있다. 변위 제어 방식은 장비의 탄성 변형량과 축 힘의 상관관계를 활용하는 방식으로, 정밀도는 높으나 수직 다관절 로봇 머니퓰레이터에서는 활용이 어렵다. 힘 제어 방식은 머니퓰레이터의 종류와 상관없이 적용할 수 있지만, 공정 조건에 따라 적절한 힘 제어값을 설정해야 한다는 단점이 있다.
- 툴의 삽입 깊이를 제어하기 위해 축 힘을 측정하는 센서의 채용은 필수적이다. 이를 활용하는 공정 모니터링 기술도 상용화되어 있다. 해당 기술은 표준이 되는 축 힘 범위값을 설정해 두면 측정되는 축 힘이 해당 범위를 벗어났을 때 작업자에게 경고를 보내거나 장비를 중지하는 기술로 구현되어 있다. 이는 공정 중 툴의 파손, 연결부의 간극 등 불량을 초래하는 상황에서 축 힘이 다르게 발생하는 특징을 이용한 것이다. 최근 인공지능 기반의 예지보전 기술이 발달함에 따라 축 힘과 축별 이송모터의 신호를 인지하여 품질 수준 예측, 결함 유형 판별 등을 수행할 수 있는 기술이 연구되고 있다.
- 용접부의 품질제어 기술로서 툴 틸트각(측면 틸트각)은 매우 중요한 기술이다. 목표로 하는 용접 속도에서 툴 형상의 변경으로 용접부 결함을 회피할 수 없을 때 활용할 수 있는 기술로, 수직 다관절 로봇과 같은 강성이 낮은 머니퓰레이터에는 필수적으로 부여되어야 한다. 공작기계 형식의 머니퓰레이터에는 용접 속도를 향상시키기 위한 부가 기능으로 활용된다.
3. 장비기술 및 시장 동향
머니퓰레이터의 유형에 따른 분류 및 특징
- 장비는 머니퓰레이터의 유형에 따라 수직 다관절 로봇 기반 장비와 공작기계 기반 장비로 분류할 수 있다. 수직 다관절 로봇 기반 장비는 작업과 설치 공간에 대한 높은 유연성을 보유하고 있으나, 제한적인 내압 사양에 의한 용접 속도와 적용 소재가 제한되며, 힘 제어 기능이 필수적으로 요구된다. 공작기계 기반 장비는 내압 사양이 높아 다양한 소재에 대해 높은 용접 속도를 구현할 수 있으며, 변위 제어와 힘 제어를 적용할 수 있다. 하지만 툴 틸트각을 부여하기 위해서는 별도의 틸트 헤드의 장착이 요구된다. 마찰교반용접 장비와 절삭 공작기계의 유사성을 활용하여 마찰교반용접과 절삭 공정을 순차적으로 수행할 수 있는 복합 장비도 상용화되었다.
수직 다관절 로봇 기반 장비
- 가반하중 500kgf급의 산업용 로봇에 직결식 스핀들을 장착한 형태가 주류이며, 직결식 스핀들 내부에 로드셀을 통한 축 힘 측정장치가 기본적으로 탑재된다. 부적절한 힘 제어 수치 입력에도 과다한 용입이 발생하지 않는 SSFSW 기술을 주로 채용한다. 내압 사양의 제한에 의해 용입 깊이 5mm 이상으로 활용하기에는 부적절하며, 알루미늄 합금 소재를 용접하는 데 적합하다.
- 독일 Kuka robotics社의 장비는 500kg의 가반하중 자사 로봇에 독일 Cytec社의 직결식 스핀들을 채용하고 있다. 선택에 따라서 1축, 3축, 6축 하중 모니터링 및 힘 제어가 가능하고, SSFSW를 위한 헤드를 구성하고 있다. 미터급의 작업 반경과 높은 완성도의 제어기술을 장점으로 국내 전기차 배터리팩 제조시장을 선점한 장비로 알려져 있다.
- 다국적 기업인 ESAB社의 장비는 자사의 직결식 스핀들과 500kg 가반하중의 로봇으로 구성된다. 지역에 따라서 다른 공급사(ABB의 600kg 가반하중 모델)의 로봇과 매칭되는 경우도 있다. 직결식 스핀들은 타 공급사의 로봇과 연동 제어가 가능하도록 기술 서비스를 제공하고 있다. 1축 하중 모니터링 및 힘 제어가 기본적으로 탑재되어 있으며, SSFSW를 위한 헤드를 구성하고 있다.
- 독일 Grenzebach社의 장비는 자사 스핀들과 로봇으로 시스템을 구성하고 있다. 공작기계 기반 장비를 생산하는 기업인만큼 시스템과 CAD/CAM 소프트웨어와의 연동 제어를 강점으로 내세우고 있다.
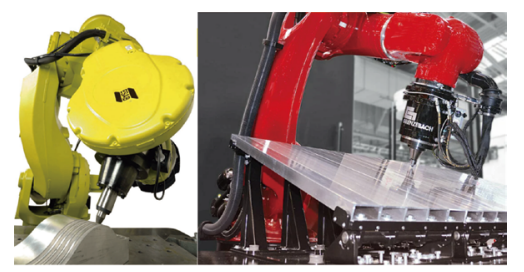
- 상술한 기업 외에도 로봇 전문기업이나 마찰교반용접 스핀들 전문기업을 중심으로 수직 다관절 로봇 기반 장비가 상용화되고 있다. 상용화된 장비로 구성된 제조 셀의 도입 비용은 약 수십억 원대이며, 툴 세트의 경우 수백~수천 달러 수준으로 알려져 있다. 국내의 경우 KEIT의 지원을 통해 산업용 로봇 전문기업인 HD현대로보틱스와 스핀들 전문기업인 카스윈이 포함된 컨소시엄의 협업을 통해 상용화를 위한 장비 개발연구를 진행하였으며, 2024년 상용화를 앞두고 있다.
공작기계 기반 장비
- 기존 공작기계와 구성적인 차이가 크게 없는 구성이며, 파생 기술을 모두 활용할 수 있다는 장점 때문에 기존 공작기계 제작사와 스핀들 제작사를 중심으로 다양한 수요산업에 활용할 수 있는 장비가 상용화되고 있다. 대표적인 기업으로는 독일의 Fooke, Grenzebach, HAGE, 오스트리아의 Stirtec, 미국의 ESAB, PaR Systems, 프랑스의 Stirweld, 일본의 Hitachi 등이 있다. 유럽 및 북미 장비는 10억 원 이내의 소형 장비부터 대형 장비까지 주문자 수요 맞춤 장비로 공급 가능하지만, 도입 비용이 높은 편에 속한다. 마찰교반용접 전문기업의 경우 기성품 형태로 마찰교반용접 툴과 기타 액세서리를 제공하면서 기술 서비스도 함께 제공하고 있다.
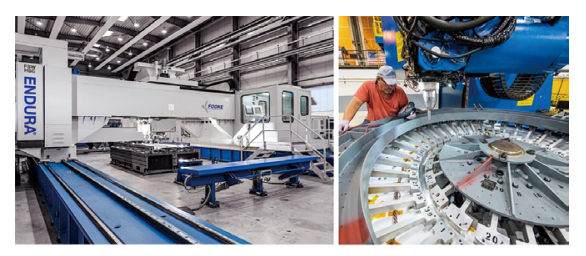
- 중국에는 Beijing FSW 등의 장비 제작사가 있으며, 유럽 및 북미 장비 대비 높은 가격경쟁력으로 세계 시장에 진입하여 점유율을 늘리고 있다. 장비 신뢰도와 기술력에 대해 저평가되는 문제를 해결하기 위해 마찰교반용접 기술을 개발한 TWI와 기술 라이선스를 바탕으로 기술경쟁력도 확보해 나가고 있다. 소형부터 중대형 라인업을 구축하고 있으며, 국내 시장에서는 국산 장비보다 점유율이 높은 상태다.
- 국내의 경우 화천기계가 30kN급 내압 성능을 가진 F1300을 출시했다. 사용자가 요구하는 용접 품질 수준에 관한 기술 지식 서비스도 제한적으로 제공하고 있다. 미터급 부품에 적용하기 위한 F4020 모델도 최근에 출시되었다.
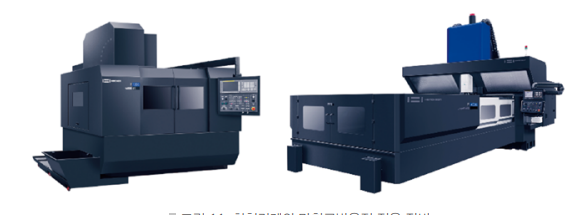
- 공작기계 기반 장비는 수직 다관절 로봇 기반 장비 대비 높은 내압 성능과 정밀도에 의해 우주·항공 분야에 활용이 되고 있다. 특히 최근 발사체의 경량화를 위하여 용융용접을 할 수 없는 경량 소재의 채용이 확대되고 있다. 이에 마찰교반용접을 중심으로 고상접합만으로 구조체를 만드는 기술을 보유한 북미의 경우 PaR Systems의 장비인 iSTIR에 대해 금수 조치를 취하고 있다.
절삭-마찰교반용접 복합기
- 북미의 마찰교반용접 기술 컨설팅기업인 Megastir社를 인수한 일본의 공작기계 전문기업 Mazak社는 절삭과 마찰교반용접을 순차적으로 수행할 수 있는 복합기 장비를 최초로 상용화했다. 상대적으로 좁은 작업 범위, 툴 틸팅헤드의 부재, 힘 제어시스템이 채용되지 않아 생산성과 품질 수준이 높지 않다는 평가를 받고 있다. 오스트리아의 Stirtec社는 대형 복합기를 출시하면서 힘 제어시스템을 채용했다.
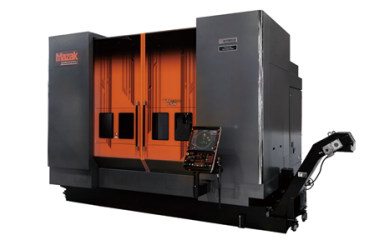
- 마찰교반용접을 수행할 때 발생하는 토 플래시와 용접 변형에 의한 형상 뒤틀림에 대한 보정이 필요한 경우 복합기의 활용이 생산성 측면에서 효과적이다. 국내의 경우 KEIT 및 KIAT의 지원을 통해 공작기계 전문 기업인 화천기계와 디엔솔루션즈(舊 두산공작기계)가 각각 소형 및 대형 복합기의 개발을 시작했으며, 2025년 상용화를 목표로 개발 중이다.
마찰교반점용접 장비
- 마찰교반점용접은 기존 장비로 스핀들의 삽입과 토출만으로 쉽게 구현할 수 있으나 출구 구멍에 의해 용접 성능이 크게 낮아지는 문제가 발생한다. 아울러 점용접이 가장 많이 활용되는 자동차의 차체 부품에 적용하기 위해서는 로봇에 거치할 수 있는 C 클램프 타입이 요구된다.
- 출구 구멍을 메워 점용접 성능을 비약적으로 향상시키는 RFSSW 기술은 동심을 가진 두 개의 회전축이 개별적으로 회전 및 병진운동을 수행해야 하기 때문에 기술적 난이도가 높은 편이며, 장비 국산화도 쉽지 않은 상태다.
- RFSSW 장비는 북미와 유럽 중심으로 개발 및 생산되고 있으며, 가장 많이 알려진 장비는 75년의 업력을 가진 독일 Harms & Wende社의 장비다. 상용화된 장비의 용접 품질이 확보되어 우주·항공 분야 및 특수 분야에 활용되고 있으나, 대량생산에 대응할 수 있는 연속 용접 성능과 신뢰성에 있어서는 개선이 필요한 것으로 평가된다.
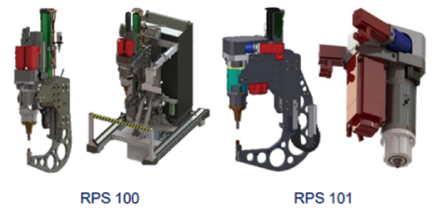
4. 적용 사례 및 파급력
우주·항공산업
- 우주발사체의 무게가 늘어날수록 실을 수 있는 위성의 크기가 작아지므로 경량화를 위하여 우주왕복선의 극저온 연료탱크 및 발사체에는 초경량 리튬 계열의 알루미늄 합금이 활용되고 있다. 대표적으로 Space X社의 Falcon 9에는 용융용접이 불가능한 소재를 사용하여 전체 구조에 마찰교반용접과 파생 기술을 활용했다. 최근 NASA, ESA, JAXA 등 다국적 협업으로 진행되는 ‘아르테미스 계획’에서도 마찰교반용접 기술이 활용되고 있다.
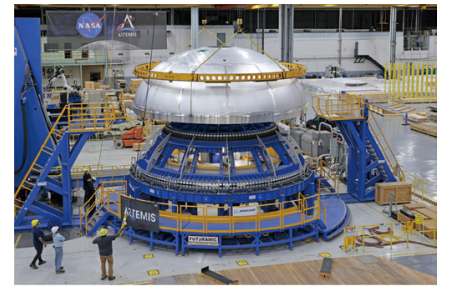

표 2. 마찰교반용접을 적용한 발사체
- 경량화된 연료탱크는 2~3m의 두께로 이면 접근이 불가한 환경 때문에 BT-FSW가 적용되었으며, Adjustable tool probe FSW, RFSSW 등이 단속 및 브래킷 용접에 활용되었다. 겹치기 용접부에 대해서는 알루미늄 합금 표면의 산화층을 용접 전에 제거하는 것이 중요하기 때문에 절삭-마찰교반용접 복합 기능을 가진 장비를 활용했다.
- 국내에서도 차세대 발사체 제작기술 및 장비에 관한 연구가 진행되고 있다. NRF의 지원으로 엔디티엔지 니어링(주)을 주관으로 하여 미터급의 탱크를 생산할 수 있는 제작 설비를 구축하고 있다. 민간 발사체 산업의 확대 및 군수산업으로의 적용 가능성을 고려하면 우주·항공 분야에 활용할 수 있는 상용화 수준의 국내 기술 향상, 그리고 국산 장비의 개발이 필요할 것으로 보이나 국내 기술과 장비의 수준이 충분히 확보되지 않은 상태다.
자동차산업
- 전기차 전환 시대 이전의 마찰교반용접 기술은 차량의 차체 및 섀시 부품의 경량화를 위한 용접기술로 적용되었다. 주로 고급 대형 차량이나 고성능 차량에 활용되었다. 혼다의 경우 알루미늄 합금-탄소강으로 구성된 이종접합 연결부에 마찰교반점용접 기술을 활용한 바 있다.
표 3. 자동차산업에서 마찰교반용접의 적용 사례
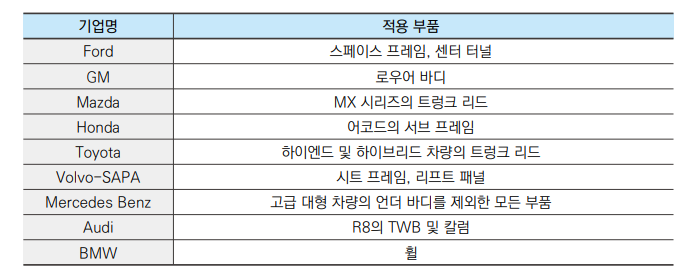
- 전기차로의 전환은 마찰교반용접 기술의 보급과 확산에 가장 큰 계기로 평가된다. 배터리를 외부로부터 격리하는 배터리팩 부품과 인버터 등 핵심 전력장치를 보호하는 케이스는 내식성과 높은 비강도, 그리고 높은 방열 성능이 요구되므로 알루미늄 합금으로 제작된다. 그래서 용접부의 높은 기밀성과 열전도도를 구현할 수 있는 마찰교반용접이 채용되었다.

- 전기차용 배터리팩은 미터급 크기와 팩당 대략 6m 이상의 긴 용접을 요구하는 반면, 3mm 두께의 박판 접합을 요구하기 때문에 수직 다관절 로봇 기반 장비가 주력으로 활용되고 있다. 다만 생산성과 정밀도 향상을 위하여 공작기계 기반 장비도 활용되고 있다. 그러나 국내 마찰교반용접 기술과 장비에 대한 저변이 준비되지 않은 상태에서 장비 대부분과 기술 시장은 수입 장비와 외국계 기업의 기술로 채워진 상태다. 소형 부품에 대한 시장도 국내 장비보다는 중국산 장비가 주로 활용되고 있다.
기타 산업
- 조선 및 플랜트에서 요구하는 부품은 10mm 이상의 후판을 활용하는 사례가 많으며, 이때 발생하는 축 힘을 버틸 수 있는 장비를 구축하기 어려워 BT-FSW를 적용하는 사례가 있다. 향후 액화수소 같은 극저온 연료를 위한 설비를 제작하는 기술로 마찰교반용접 기술의 적용이 기대된다.
- 또한 알루미늄 합금과 조합되는 이종접합 연결부로 구성되는 각 산업의 부품을 제작하는 데 마찰교반용접 기술의 확산이 예상된다. 기존 이종접합 연결에 활용하는 기계적 체결과 접착제의 조합 대비 높은 기밀성과 신뢰성을 활용하는 사례가 증대될 것이다.
5. 정리 및 시사점
정리
- 마찰교반용접은 고상용접의 한 종류로, 회전하는 툴에 의해 소재를 마찰가열 및 교반하여 용접부를 생성하는 기술이다. 이 기술은 주로 알루미늄 합금의 용접에 활용되며, 마그네슘 합금, 구리 합금, 티타늄 합금과 탄소강과의 이종접합도 가능하다. 마찰교반용접 장비는 소재에 접촉하여 용접을 수행하는 툴, 툴을 고속으로 회전시키는 스핀들, 그리고 툴을 이송하고 소재에 삽입하는 머니퓰레이터로 구성되어 있다.
- 마찰교반용접의 툴은 프로브와 숄더로 구성되며, 이들의 형상은 용접부의 품질과 생산성을 결정한다. 이 기술의 제한점을 해결하기 위해 다양한 파생 기술이 제안되었으며, 이들 중 일부는 툴의 삽입 깊이를 제어하는 기능을 포함한다. 마찰교반용접 기술의 품질제어에는 툴 틸트각이 중요하며, 이는 용접 속도를 향상시키는 데 활용된다.
- 장비는 머니퓰레이터의 유형에 따라 수직 다관절 로봇 기반 장비와 공작기계 기반 장비로 분류된다. 수직 다관절 로봇 기반 장비는 작업과 설치 공간에 대한 높은 유연성을 갖지만, 내압 사양이 낮고 힘 제어 기능이 필요하다. 공작기계 기반 장비는 높은 내압 사양과 변위 제어 및 힘 제어를 적용할 수 있지만, 툴 틸트각을 부여하기 위해서는 별도의 틸트헤드의 장착이 필요하다. 마찰교반용접과 절삭 공정을 순차적으로 수행할 수 있는 복합기 장비, 마찰교반점용접 성능을 향상시키는 리필 마찰교반점용접 장비도 상용화 상태다.
- 우주·항공산업에서는 마찰교반용접 기술이 우주발사체의 경량화를 위해 활용되며, 이는 Space X의 Falcon 9와 ‘아르테미스 계획’ 등에서 볼 수 있다. 자동차산업에서는 전기차로의 전환으로 배터리팩 부품과 인버터 등의 핵심 전력장치 보호에 마찰교반용접 기술이 활용되고 있다. 그러나 국내 마찰교반용접 기술과 장비는 아직 충분히 확보되지 않은 상태이며, 대부분 국내 장비와 기술시장은 해외 기업이 선점한 상태다.
- 조선 및 플랜트산업에서는 10mm 이상의 후판을 활용하는 부품 제작에 마찰교반용접 기술의 적용이 늘어날 것으로 예상되며, 액화수소 시대로의 전환에서 확산이 전망된다.
시사점
- 마찰교반용접 기술이 개발된 지 30여 년이 지났으며, 특허 소멸 후 본격적으로 준비가 가능한 기간은 10년 정도다. 10년의 세월은 국내 공정 및 장비기술을 준비하고 관련 저변을 구축하는 데 부족한 시간일 수도 있다. 하지만 급격하게 찾아온 사회와 경제의 변화로 마찰교반용접 기술의 수요가 증가하고 있고, 이러한 환경에서 마찰교반용접 기술과 관련한 이권을 선점한 곳은 해외 기관과 기업들이다.
- 해외 마찰교반용접 기술과 관련한 연구기관과 장비기업은 우주·항공 및 조선 분야의 수요를 통해 기술과 장비의 내실을 쌓아가고 있다. 생산 대수와 적용 범위가 넓지 않은 산업임에도 장비기업은 해당 장비를 개발하는 데 투자를 망설이지 않고 있다. 연구기관도 마찬가지다. 이는 새로운, 그리고 가능성이 있는 (실패할 수도 있는) 기술에 대한 가치를 충분히 지급하는 사회·경제적인 구조에 의한 것이다.
- 미래에 어떠한 기술이 필요할지 예측하기란 어려운 일이다. 불확실한 예측을 믿고 미래기술에 투자하는 것은 실패를 용납하지 않는 사회에서는 부담이 크다. 마찰교반용접 기술도 전기차 시대가 도래하지 않았 다면, 그리고 국내 기업들이 시장에 전폭적으로 진입하지 않았다면 국내에서는 천대받는 기술로 분류 되었을 것이다. 그렇다면 기술개발 기반이 점차 사라지고 향후 수요 발생 시 외산 기술에 의존할 수밖에 없는 기술로 분류될 것이다.
- 마찰교반용접 기술에 대한 공정기술과 장비기술에 대한 개발은 늦었지만, 현명한 연구개발 전담 기관의 판단으로 곧 상용화를 앞두고 있다. 외산 기술과 장비 대비 시장 경쟁력을 충분히 갖춘다면 저렴하게 제작하는 기술이 필요해진 전기차시장에 동조하여 외산 기술의 의존 없이 국가 경쟁력을 향상시킬 수 있는 계기가 될 것이다.
출처 및 참고자료
1. The Welding Institute의 홈페이지, www.theweldinginstitute.com
2. ISO 25239-1~5:2020, Friction stir welding–Aluminium, International Organization for Standardization.
3. ISO 18785-1~5:2018, Friction stir spot welding–Aluminium, International Organization for Standardization.
4. AWS D17.3/D17.3M:2016, Specification for Friction Stir Welding of Aluminum Alloys for Aerospace Applications.
5. “마찰교반용접의 기초”, 이원식, 한국과학기술정보연구원.
6. KS D 3753:2008, 합금 공구강 강재, 한국표준협회.
7. KS D 3522:2008, 고속도 공구강 강재, 한국표준협회.
8. “The mechanism of rotational and non-rotational shoulder affecting the microstructure and mechanical properties of Al-Mg-Si alloy friction stir welded joint”, Hua JI. et al.(2020), Materials & Design, Volume 192, 108729.
9. “Friction stir welding of AZ31 magnesium alloy: A review”, Ashish M. DESAI, et al.(2021), materialstoday: PROCEEDINGS, Volume 47, Part 19, pp. 6576-6584.
10. 「마찰교반용접 기술의 항공우주분야 응용 동향」, 정현호 외(2014), 항공우주산업기술동향, 12권 2호, pp. 158-165. www.kari.re.kr/download/viewer/1549535222864/index.html.
11. “Understanding Friction Stir Welding”, A.C. Nunes, Jr.(2018), NASA/TM-2018-219854. ntrs.nasa.gov/citations/20180002399.
저자 : 이병현 뿌리 PD / KEIT 천현필 수석(보) / 한국생산기술연구원
'산업기술' 카테고리의 다른 글
민수기술 기반 군 유무인복합체계의 기술 발전 방향 (0) | 2025.02.12 |
---|---|
2024년 반도체산업 시장 및주요국 정책동향 (0) | 2025.02.10 |
평판 OLED를 이용한 공간 표시 차세대 디스플레이 기술 (0) | 2025.02.10 |
스마트섬유 기술 동향 및 전망 (0) | 2025.02.09 |
극저온 냉동기의 활용 사례 및 개발 동향 (0) | 2025.02.09 |
댓글